paperwear
Visit the Website
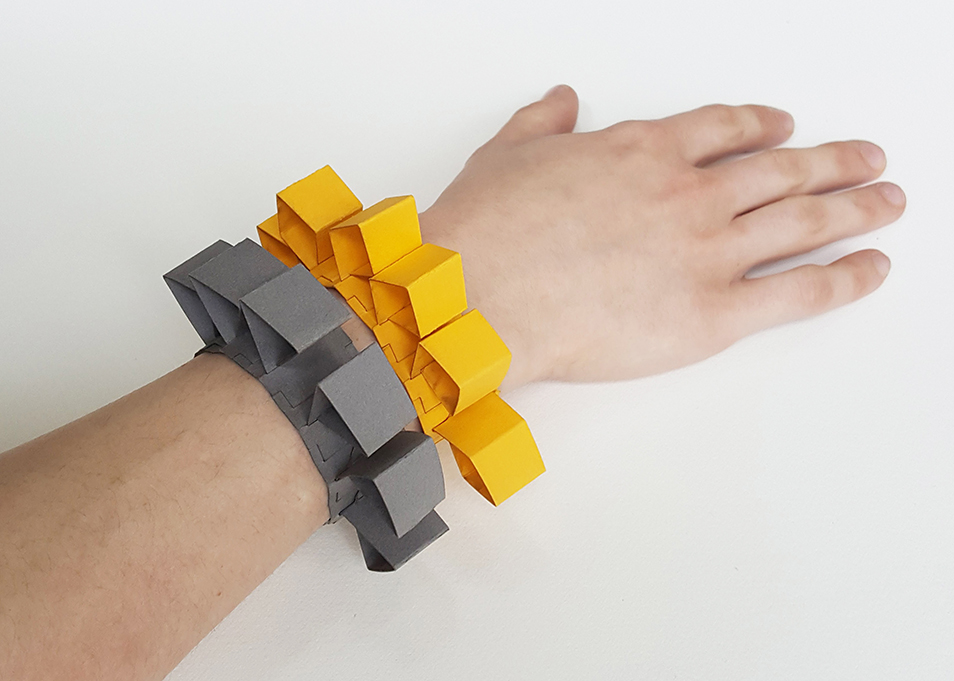
This was an exploration of parametric jewelry design using paper.js. I had previously designed 3D printed earrings and received positive responses to those earrings. When I showed them, people were enthusiastic about how the earrings were inexpensive, customizable, and unusual. The printed earrings are not precious and are easy to put on, and many people who do not usually wear jewelry were excited to test them.
In designing customizable jewelry, I wanted to create a product that was similarly fun and accessible. I intended to incorporate inexpensive materials, easy experimentation, and fun results. Paper.js offers programmable vector graphics, and so the .svg results may be taken directly to a cutting machine. It's also web-based, and I hope to eventually offer these patterns online.
I have a background in flat-pack packaging design, and since then, have wanted to explore jewelry design using sheet stock. There are many designers working with sheet metal and fold-up design aesthetics: Mirjam Hiller makes incredible and delicate pieces by hand cutting colorful aluminum. Larah Nott works in a much more industrial aesthetic, directly referencing architecture and fold-up packaging.
With a rise in makerspaces and hackerspaces, and the increasing affordability of machines like laser and waterjet cutters--previously out of reach to a consumer audience--it is now practical to design and distribute digital fabrication files for a casual audience. Thingiverse has used this model for distributing 3D print files.
Flat-pack design has been used by Nintendo Labo to encourage play, customization, and experimentation in a gaming context. Pepakura enables users to generate 'unfolded' paper templates from 3D models.
Sheet metal jewelry and flat-pack design translate well to computational design. The designs may incorporate parameters and user input to generate diverse forms. The .svg files from a paper.js program are easily prototyped in paper or plastic with a laser cutter, or may be taken to a waterjet cutter and cut out of metal. The format both encourages experimentation and permits a high level of finish--a desirable range for parametric wearables.
Cube Chain
The cube necklace design offers three user input options: a drawing for the tab shape, the width of the cubes, and the number of cubes in the chain.
A range of cube outputs from varied inputs
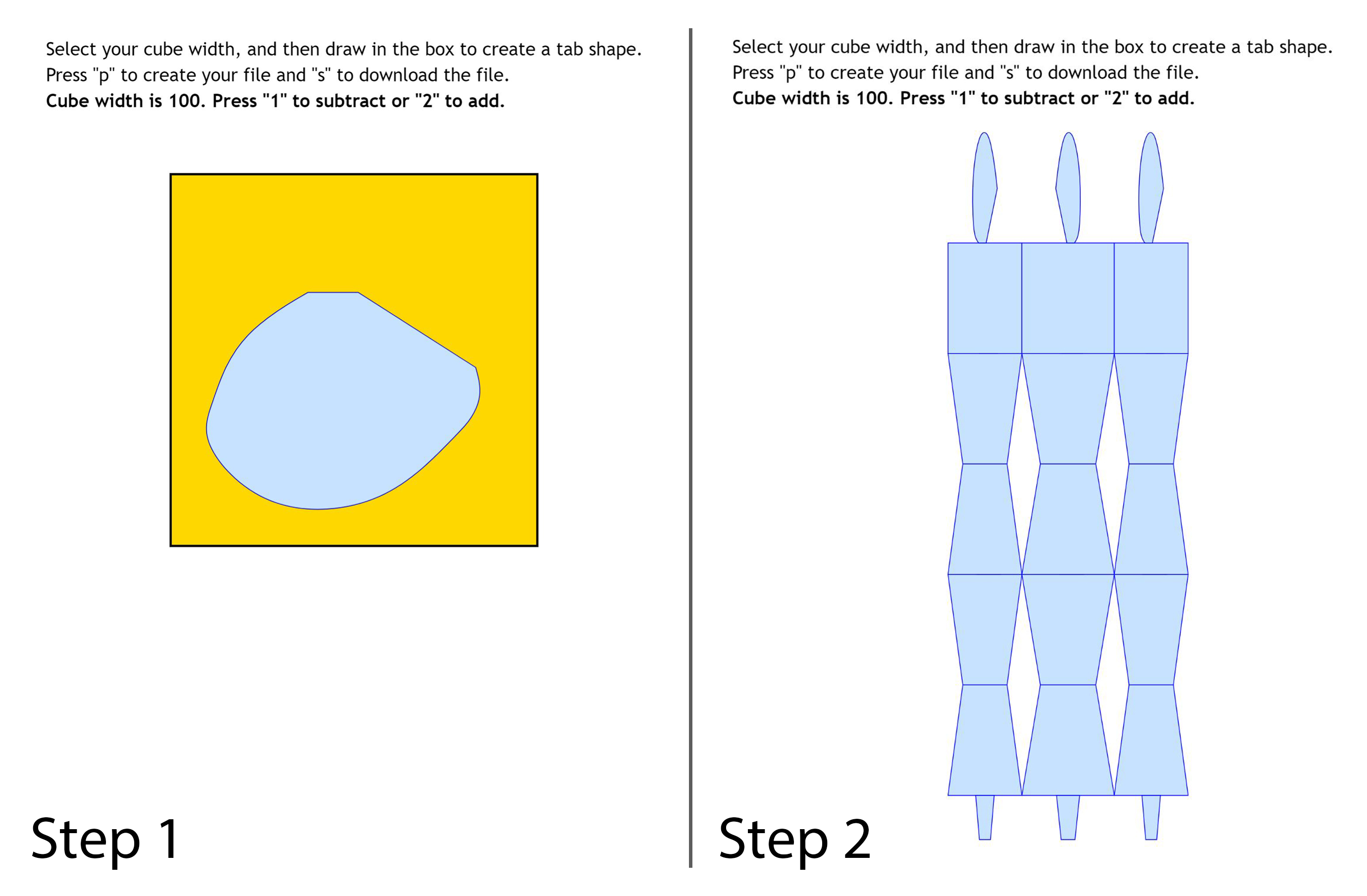
File generation process: drawing input with key controls for number inputs.
Wave Necklace
The wave necklace is created with user drawing input. It generates mirrored wave links for variation, and also offers a preview of the final layered result.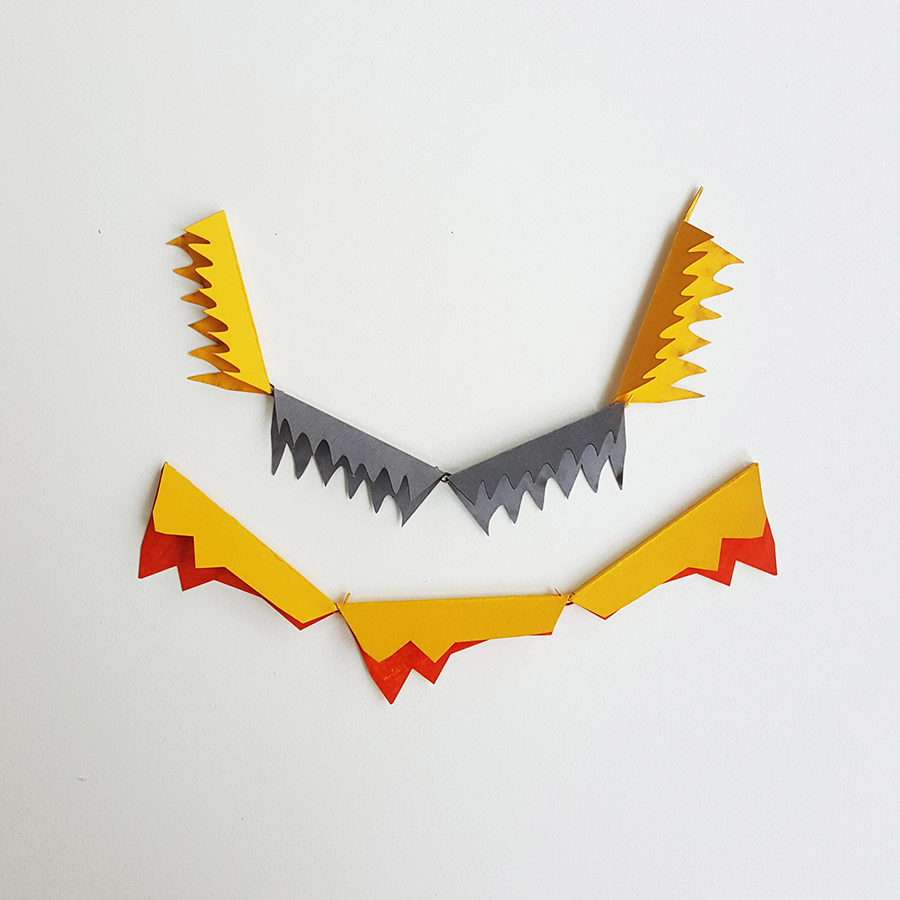
Two variations on the wave necklace
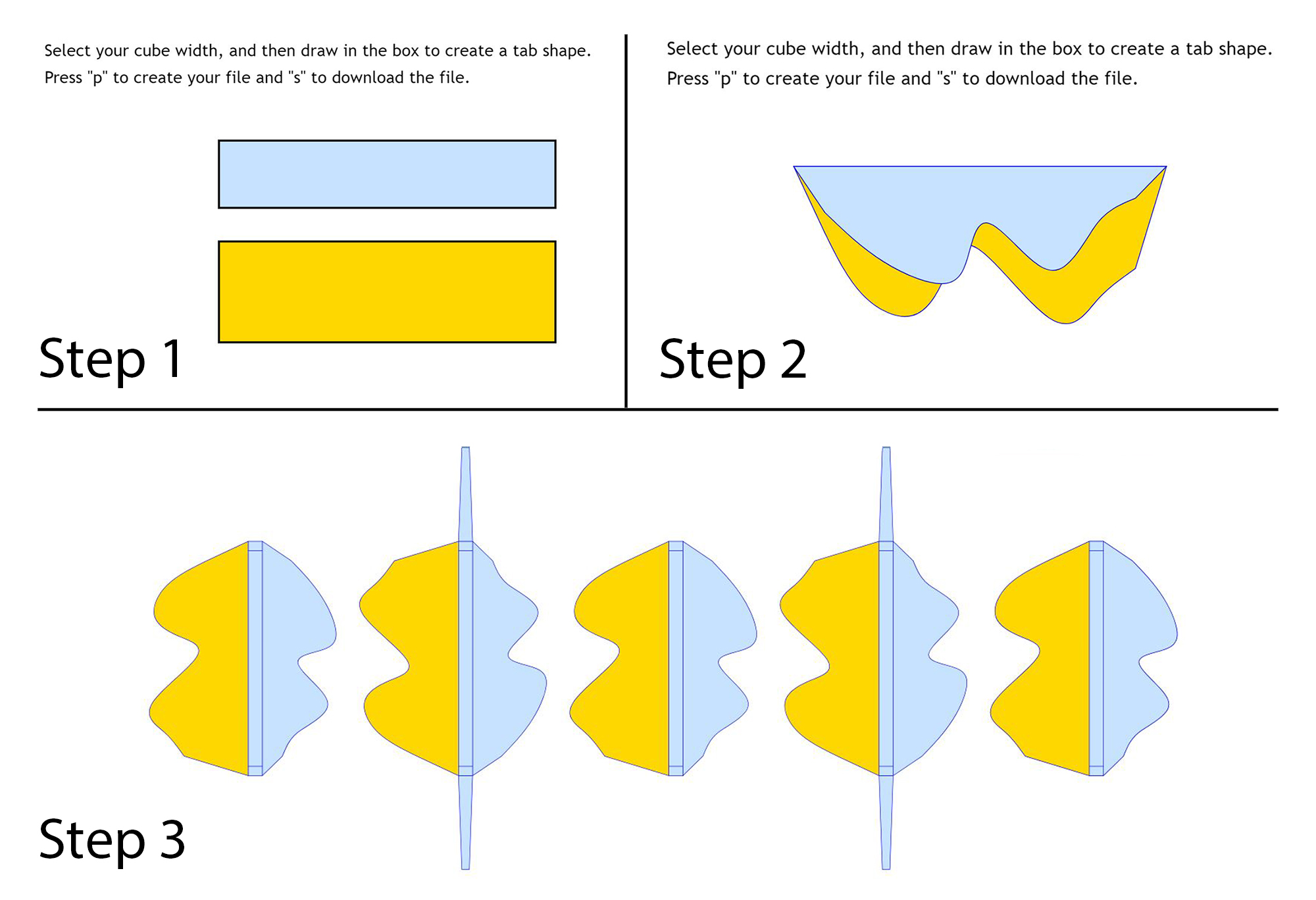
A three-stage interface with drawing and keyboard controls
Curl Bracelet
The curl bracelet is composed of several links. It includes user input for the shape of cutout holes on the outer blocks, and the final diameter of the outer blocks.
A few variations on the curl bracelet, in plastic and paper
Updated interface with GUI controls
Material Experiments
I tested my design outputs in a few different papers--a thin craft paper, a heavier cardstock, and a thick board. The cardstock was the most successful, and most of the pieces in the images here are created from laser cut cardstock.In addition to paper, I tested polypropylene (see white bracelet in image above). I wasn't able to cut plastics with the laser cutter, so cut these links by hand. The polypropylene worked well and looked nice, however, it was prone to tearing. I'd like to test more plastics for durable material options. Plastic and natural fibers are wearable for those with metal allergies, and so I'd like to offer durable, finished alternatives to metal for the final product.
I made some waves links out of aluminum, cutting them by hand. The aluminum was difficult to bend cleanly; metal would bend better with perforation lines. In future iterations, I'd like to have user controls that would customize the patterns for different materials. Metal settings could include perforation lines, and paper settings would have different tab structures. Tab slots could be wider or narrower depending on material thickness.

Aluminum links
Future Iterations
I'd like to add better user interfaces for these designs, and put them into context on a website, including assembly instructions. All three designs have more parameters that I'd like to expose, for example, smooth vs. angled drawing curves.Further materials testing would be useful, and I will create some finished pieces out of waterjet cut metal. While testing the physical products, I'd refine the designs themselves and develop size guidelines for each design.
Currently, the designs do not incorporate effective clasps, and so must be attached to metal chains. The final versions should include elegant and easy-to-use clasps.